DEMOLITION & THE ENVIRONMENT
On average, over 95% of all waste that arises from a demolition project can be recycled. That’s just one way that demolition works can be tailored to protect and preserve the surrounding environment. Read on to find out all the ways you can ensure environmental protection during your demolition project.
Demolition projects come in all sizes. Demolition contractors work to ensure materials, waste and the environment are considered at every stage of a project.
See some of our favourite demolition industry facts and stats.
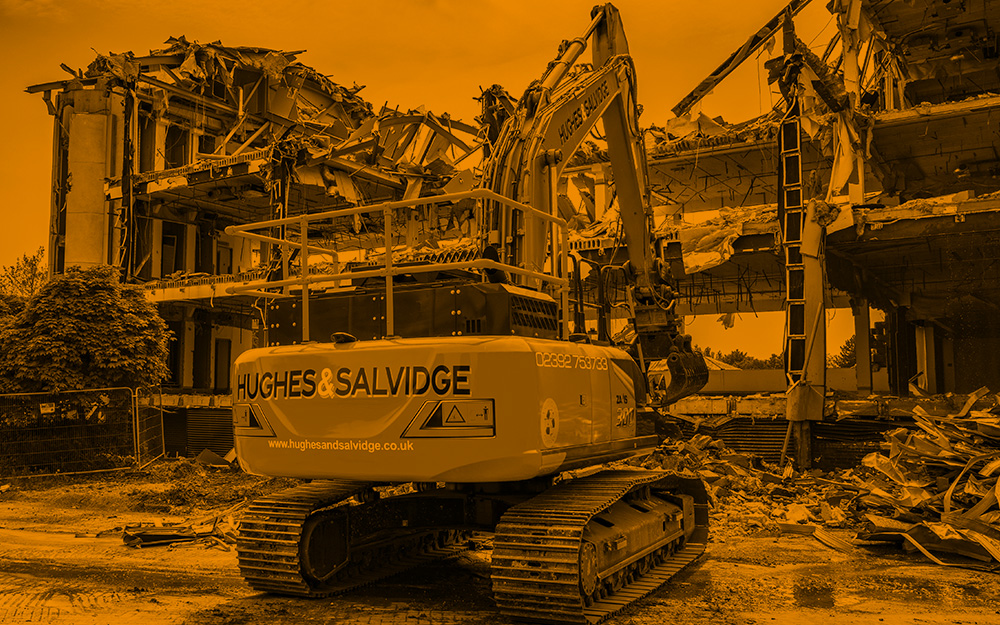
25%
of all waste generated in the EU is attributed to construction and demolition waste, at an estimated 120 million tonnes.
96%
or above, recycling rate is regularly achieved by the UK demolition industry.
STAGE 1-ECOLOGY
Projects located near to, or adjacent to, conservation areas, waterways or areas of environmental interest require permissions from the Environment Agency prior to commencement of works.
A relationship with the Environment Agency is maintained throughout the duration of the project and continued upon completion to ensure permissions and regulations are adhered to.
Ecological surveys and reports are conducted prior to demolition taking place and the contents of these documents provide information for demolition contractors to provide a method of works. These are produced by specialist ecologists and identify species that require re-homing or protecting including bats, birds, newts and frogs. Flora and fauna surveys are also conducted at this early stage to identify plants and vegetation that may require protection. This provides valuable information for producing Environmental Management Plans and Risk Assessments and allows for Tree Protection Plans to be drawn up.
Standard tree protection involves Heras fence panels, to provide stability, placed around the footprint of a tree to act as an exclusion zone to prevent collision with machinery and equipment.
STAGE 2-ASBESTOS REMOVAL
As with the Ecology reports, Asbestos surveys and reports are conducted by approved analysts prior to any demolition activity commencing on site.
Asbestos materials are then removed by trained, experienced teams licenced by ARCA and the HSE. Asbestos removal is undertaken in an isolated environment to prevent materials escaping and contaminating the surrounding environment. The hazardous materials are securely bagged and disposed of at licenced waste facilities nearby.
Throughout a demolition project, previously undiscovered asbestos can be found, leading to demolition works halting in that area of a site. This is isolated and then dealt with by qualified teams.
STAGE 3-SOFT STRIP
The soft-stripping stage of a demolition project involves removing all non-structural items within a building or structure, including fixtures and fittings, electrical cables, internal walls and ceilings, and any temporary internal structures.
This stage can sometimes be completed as a standalone project in preparation for a building refurbishment or repurpose.
The items removed during a soft strip can often be repurposed or recycled. Office equipment can be sold, redistributed or donated to charity. Materials such as timber, steel and glass can all be recycled, considerably reducing the volume of materials sent to landfill.
STAGE 4-DEMOLITION
The three methods to demolish a structure are by mechanical means, by hand, or by using explosives.
The method of demolition varies from project to project and takes into consideration the type of building or structure, the materials it is constructed with, any hazardous materials that are present, and the surroundings of a site which can include residents, occupied and in-use buildings, waterways, roadways, green areas, and listed buildings. Risks are also used to determine the method of demolition, including any risks to the surrounding environment.
Noise and vibration are part and parcel of demolition works and can affect the site surroundings, disturbing residents and local wildlife. Noise is kept to a minimum by:
-Using the correct plant and equipment for specific tasks
-Ensuring plant and equipment are fully maintained
-Using the ‘quietest’ method when both demolishing structures and removing hardcore and concrete
-Leaving part of the external envelope of buildings intact whilst removing materials. This is determined by structural stability of buildings as demolitions proceed
-Ensuring works are only carried out within agreed working hours
Dust regularly presents itself as a hazard during demolition works. It can be at best a nuisance and at worst escape into waterways, affect green areas and wildlife, and disturb residents. Dust is controlled by damping down, using temporary water supplies around a site or via fire hoses and sprayed directly onto the workface and/or piled demolition arisings. Protective booms and spill kits are used to prevent damping down water, and fuel or chemicals, running into nearby waterways or drains. Other machinery, such as a Dust Boss Water Curtain, can be used, minimising dust and minimising the amount of water used in controlling dust.
STAGE 5-CONCRETE CRUSHING
Crushing demolition arisings on-site offers a range of environmental, logistical and financial benefits.
It reduces pollution by drastically minimising traffic movements to and from the site, keeps concrete debris out of landfill and the aggregate produced provides the construction site with a ready-made piling mat material along with other applications including a substitute for virgin aggregates.
Crushing is stringently controlled on site with noise and dust kept to a minimum.
All crushing plant have bespoke sprinkler systems contained within the plant and stockpiles of raw product and finished product are dampened down regularly.
STAGE 6-RECYCLING
The majority of demolition arisings can be recycled, with the exception of hazardous materials such as asbestos.
This minimises the amount of arisings going to landfill and results in a recycling rate of over 90% from demolition projects.
In order to achieve a reduction in material to landfill, the 4 R’s process is used to minimise disposal requirements:
Reduce, Reuse, Repair, Recycle
Typical recycled arisings are:
Brick, Concrete, Blockwork, Tarmac,
Timber, Plasterboard, Glass, Metals,
Paper, Cardboard, Plastics, Lighting Tubes.
DEMOLITION PROJECTS ACROSS THE UK
Hundreds of demolition and decommissioning projects occur across the UK each year. We’ve had our hand in a fair few, find out how we deliver bespoke services to each project, and what we do to minimise our environmental impact.
Company: Former LG Factory
Location: Newport, Wales
Facts for this project:
10,000 tonnes of crushed concrete left on site for re-use in future development.
99.7% waste recycled.
Bunded diesel tank used on site to avoid transporting fuel to the generator.
No spillages.
This project was situated in an industrial complex which was constructed in the mid 1990’s as a base for the LG Electronics Group.
The site had been split into discrete zones of development, which included the redundant main Central Utilities Building, a large steel structure, a water treatment area with a live water main and a water storage area.
The industrial park itself was still operational during the demolition works and adjacent users were served by live services passing through the contract site.
Although the site only had a light flow of traffic on a daily basis, the impact of our operations had to be taken into consideration.
Maintaining the operation of the raw water main to an adjacent data centre was a critical requirement and Hughes and Salvidge erected a scaffolding support platform under a section of overground live main to give it added stability. We also had to ensure that dust and other debris were suppressed to protect the surrounding environment.
Hughes and Salvidge achieved a high rate of recycling of plant and materials on site, with minimal waste being sent to landfill.
Company: Sheffield City Council
Location: Sheffield
Facts for this project:
River Don and Sheffield Canal ran adjacent to project site.
Control measures put in place to protect the castle moat and culvert.
700 tonnes of general waste removed from site – 97% of which was recycled.
All concrete crushed and left on site for re-use.
All steel removed from site and recycled.
Overall recycling rate 99%
This exciting project was part of Sheffield City Council’s wider plans to revamp the city and unlock the history that has been hiding below the old market buildings.
Castle Markets in Sheffield, South Yorkshire, closed its doors in November 2013 as the new Moor Market opened in the city. The former market buildings sat on the former site of Sheffield Castle itself.
The demolition work began with asbestos removal followed by a soft strip of the old market buildings. The super structure was then demolished down to the concrete so that a full archaeological excavation of the remaining castle site could take place to expose and examine the remains.
The market’s retaining wall remained as it held back the hill on which the castle was built. The Castlegate site is of huge historical interest but the full extent of the surviving castle ruins was not fully known at the early stages of the works.
The project was a huge step forward in Sheffield City Council’s plans to regenerate this part of the city centre, which included the rediscovery of Sheffield’s lost castle and the creation of new green spaces for families and visitors to enjoy.
A new park was designed to allow the castle remains to be conserved and interpreted. Initial designs for the site incorporated the three sections of the castle’s remains that were already known to exist.
Sheffield Councillor Leigh Bramall said the Castlegate area could become "an area of real historical significance for visitors, a green area where leisure pursuits can be enjoyed, and an area where vacant buildings are being regenerated and brought back into use".
Company: Heathrow Airport
Location: Heathrow
Facts for this project:
Heathrow Airport aim to become a zero-carbon airport by 2050.
Over 98% of waste recycled.
All airside vehicles Euro 5 or Euro 6 emission standard.
Over 78million passengers annually.
Nearly half a million aircraft movements annually.
Hughes and Salvidge are the only demolition contractor to have a permanent on-site presence at Heathrow Airport, having worked there for over 20 years. The extensive and challenging projects undertaken have led to further works at London Gatwick, London Stansted, and Manchester Airports.
Previous projects include:
Pier 7 Service Removal, Terminal 3
The scope of works involved the removal of all services, plant rooms and roof coverings from the Pier 7 roof and the Port Health plant rooms.
Hughes and Salvidge set-up site with scaffolding to the entire Pier. This acted as both access and edge protection whilst the roof works were taking place.
All larger items of plant were craned down from the roof. This work involved night works and the closing of airside roads and stands in coordination with Heathrow Airport Operations.
Lifting of plant was planned and executed in short windows of time and were completed ahead of schedule.
The project involved weekly planner meetings, 5-week look-ahead meetings, and Yellow Jacket reporting and inspecting. These meetings were attended by the Project team and Health and Safety team, the Client’s representative and any other necessary stakeholders.
All works were carried out in collaboration with Mechanical and Engineering isolations and installations and re-roof covering.
Pier 3 Enabling Works, Terminal 1
The scope of works included the demolition of 4 airbridges back to the rotunda and 1 fixed link bridge back to the Pier in order to enable re-routing of airside roads prior to main demolition works commencing.
Prior to commencing the demolition works, each airbridge was secured in its own compound, to carry out the works safely and to store skips.
The airbridges were sealed by foxed ply sheeting within the Pier to prevent access and leading edges. Hughes and Salvidge employed Central Hydraulics to decommission each airbridge, drain down the oils and issue a clearance certificate for demolition.
Hughes and Salvidge brought a 45t demolition excavator to site during the night in order to avoid the daytime access restrictions at the airport. Each airbridge was demolished by mechanical means with all arising material loaded in Hughes and Salvidge-controlled skips and bulkers in the relevant streams in order to eliminate the risk of Foreign Object Debris (FOD).
The fixed link bridge was prepared by operatives from MEWPs over a week of night work. It was craned down in one night ready for dismantling by machines.
All lifting works were carried out to Heathrow Airport Ltd lifting permits and procedures.
100% recycling rate was reached on this project and each area handed back to the client for re-use as they were completed.
Old Control Tower, Heathrow Airport
The Old Control Tower was a 9-storey building at Heathrow Airport demolished to make way for new roads as part of the Terminal 2 redevelopment.
A high-profile project, the works had many constraints due to the location of the building.
Situated within one of the world’s busiest airports, adjacent to Heathrow Airport Central Bus Station (the UK’s busiest) and with HTHW (high temperature hot water) mains running in ducts under the entire structure including the footprint of the tower.
Well-practiced airport procedures were used to minimise/eliminate disruption and protect the general public, staff and airport from debris and dust.
Prior to structural demolition, adequate approved methods of protection to the remaining HTHW runs were put in place.
600mm of Filcor material was placed on top of the duct covers. On top of this 18mm staggered plywood joints were positioned. Before the excavator was allowed to carry out any demolition or removal of demolition arisings, the position of the duct was marked out to ensure that the excavator did not travel on this area. This was maintained throughout the demolition process.
Vibration monitoring was undertaken within the ducts to continually monitor for any movement or impact. All works were completed safely and on time, without damage.
Heathrow T2B Phase2 Europier
This project required the centre element of the pier to be left in situ and operational and the wing sections to be removed. As with all airside projects at London Heathrow Airport, the demolition and construction programmes were time and cost critical.
On this particular scheme, we identified an alternative method of deconstruction. Instead of dismantling the pier section by section, we devised a method of lifting the entire roof sections by crane at night for processing on the apron level during the day.
The airport has stringent controls for working airside and we identified that to work at night was a quicker and more cost-effective option. The result was a programme saving of 2 weeks on a 20-week programme.
As we were able to process the arising material in house and in a more structured method on the apron, this maximised the value of metal arisings by waste streaming the ferrous and non-ferrous materials for further recycling.
Company: Versalis ENI
Location: Southampton
Facts for this project:
Over 40,000-man hours worked with no accidents or environmental incidents.
Located adjacent to Calshot Marshes and Southampton Water.
16,500+ tonnes of metal removed from site and recycled.
Over 90% recycled despite excessive rubber and asbestos present.
10,000m³ of concrete crushed and used on site as backfill.
Hughes and Salvidge completed our role of Principal Contractor for the decommissioning and demolition of this 54-acre site in March 2016.
The scope of work on this project included the removal and disposal of all asbestos, all process and storage equipment, all buildings and structural steelwork, piping (cleaning as necessary) and all above ground concrete structures, bund walls, RFC frames and similar items, including the cleaning, removal and disposal of all tanks/vessels.
We delivered the work through a 3-phased plan.
Phase one: asbestos removal, secondary chemical clean and recycling.
Phase two: plant dismantling, demolition of structures and processing of arisings.
Phase three: site clearance, making safe of site and finally completion of activities and sign off.
When working on hazardous sites, such as this former chemical site (formally manufacturers of synthetic rubbers), the management and control of environmental risks are heightened, simply due to the nature of the works previously carried out there.
The environmental risks on this project were further increased due to the closeness of Calshot Marshes and Southampton Water.
To ensure the control of environmental risks, URS produced an Environmental Management Plan on behalf of the client to ensure the impact on the environment was carefully considered, controlled and kept to an absolute minimum. Hughes and Salvidge were responsible for implementing and maintaining the control measures throughout the project.
In summary our environmental control measures included:
Erecting full height access/protection scaffold clad with debris netting or monaflex on specific buildings.
Carrying out a search for any hazardous substances or products that could contaminate adjacent waterways and removing them to a safe containment area.
Deconstruction of buildings in sequence, providing a safe, controlled system of work.
Establishing spill kits, including socks and booms.
Implementing a monitoring system to inspect the watercourse.
Ensuring dust suppression waters were contained in the boundary of the site.
Maintaining the 54db noise limit set due a SSSI (Sites of Specific Scientific Interest) being adjacent the site.
Monitoring vibration to minimise disruption to the surrounding area.