10 tips for demolition site safety
Luke Gould 12th September 2024
We prioritise safety in all we do, following strict safety protocols throughout every project from start to finish. This ensures the safety and wellbeing of our customers, staff and the general public, whilst also ensuring adherence to any relevant regulations.
Our well-established SiteZone Proximity Warning System protects site workers using radio frequency identification (RFID) technology. All our plant is fitted with SiteZone RFID detectors, while site workers have RFID transponders fitted to their hard hats.
This means that if a site worker breaches the dangerous proximity zone of a vehicle, both the worker and driver receive a 'proximity warning'. The RFID tag vibrates, making the site worker aware of the vehicle, while the driver is alerted by sound and flashing lights in the cab of the vehicle. This two-way system ensures that safety is never compromised.
At Hughes and Salvidge, as well as following the laws set out for demolition safety, we also follow these 10 tips to keep everyone safe on site.
1. Be asbestos aware
Refurbishment and Demolition Asbestos Surveys must be carried out before any demolition work can take place, and any licenced or non-licenced asbestos found must be removed in a safe and compliant manner.
At Hughes and Salvidge, we employ independent UKAS-approved analysts to undertake air sampling/fibre counting and bulk sampling in full compliance with EN450001. Only once all licenced and non-licenced asbestos has been removed, can the demolition phase of the project begin in that area. Even then, all our operatives are UKATA asbestos awareness qualified, meaning that if hidden asbestos is discovered, our staff are qualified to recognise the material. Operations will then be brought to a halt in that area until the asbestos has been sampled and, if confirmed as asbestos, safely removed.
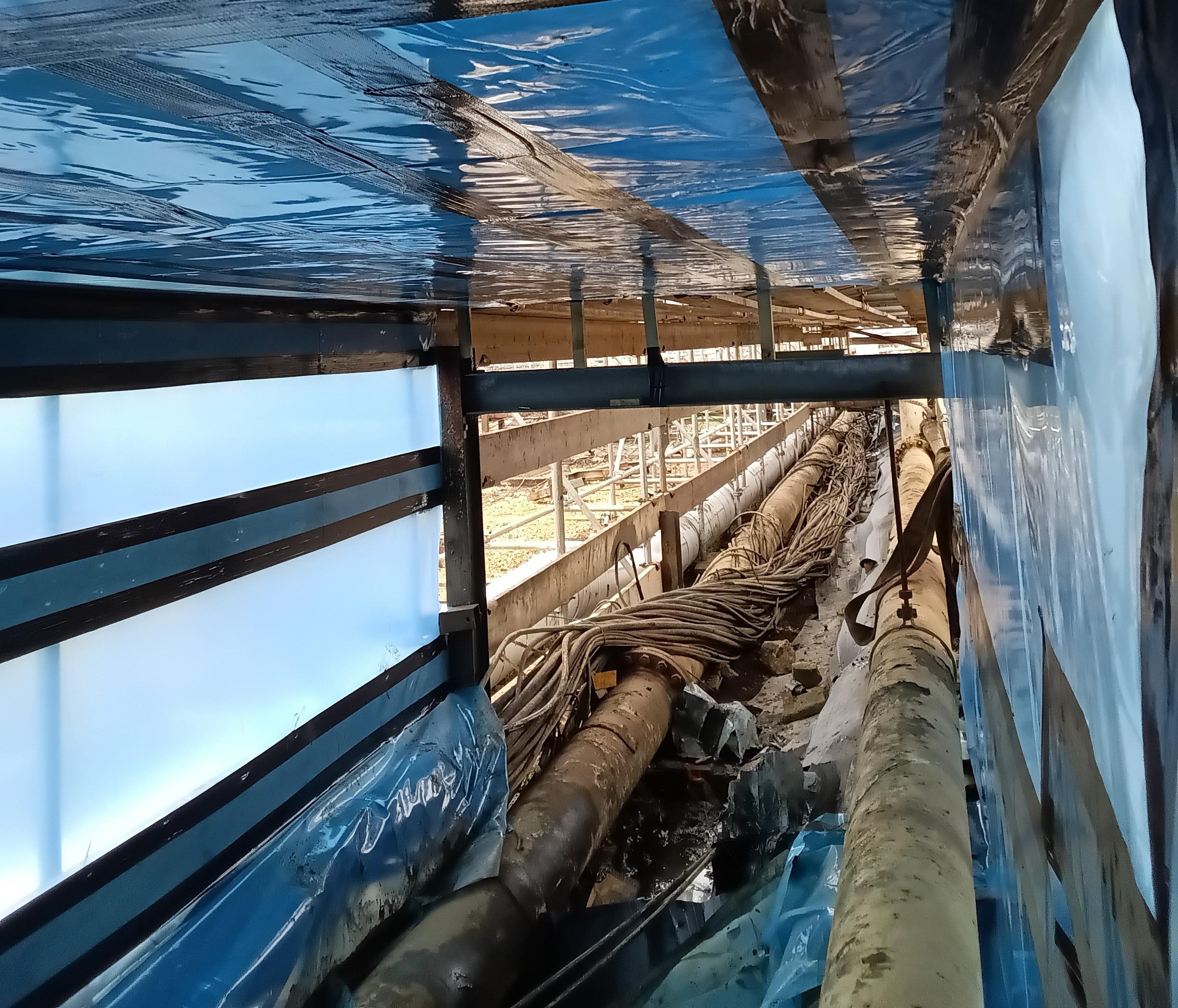
2. Wear PPE at all times
During demolition, it’s vital for all employees to wear the correct Personal Protective Equipment (PPE). As a minimum, 5-part PPE must be worn at all times on site by all operatives, including:
- Hard hat
- Safety glasses
- High-visibility vest/jacket
- Safety gloves
- SP3 boots
Our Safety Health Environment and Quality (SHEQ) Department manages the distribution of PPE to all of our operatives, ensuring we comply with British Standards and other relevant standards.
The required standards of PPE can vary, depending on the project being undertaken or a client’s specific requirements. We ensure that all our PPE satisfies each circumstance.
All of our PPE is also compliant with HSE regulations, and we supply operatives with any specialised PPE outside of the basic 5-part, for example, face masks, welding masks, fire-proof overalls, Kevlar gloves, or anything else needed to safely carry out a specific task.
The stringent management of our PPE store by our SHEQ department allows the correct PPE to be allocated to the correct project, without delay or risk to the safety of any personnel.
3. Prevent accidents with training, qualification and experience
Any staff working on a demolition site must have the appropriate qualifications, training, and experience. Regular health and safety training is needed to keep employees’ knowledge up-to-date and to help reduce the risk of accidents. To ensure we complete projects safely and to the highest standards, we work to BS6187:2011 and NFDC best practice standards, placing particular emphasis on training to keep our techniques and working practices current.
All employees have the appropriate qualifications and experience for the assigned tasks they undertake, and our site teams are closely monitored by Site Managers and Supervisors at all times. All our staff have a range of qualifications relevant to their role:
Directors: IDE Membership, NEBOSH, NVQs, CSCS and CPCS
Contracts/SHEQ/Site Managers: IDE Membership, CMIOSH, IOSH, NEBOSH, SMSTS, NVQs, CSCS, CPCS, CITB, CCNSG, and ARCA.
Site Supervisors: SSSTS, NVQs, CSCS, CPCS, CITB, CCNSG, and ARCA
Site and Plant Operatives: NVQs, CSCS, CPCS, CITB, CCNSG, and ARCA
To support this portfolio of staff qualifications, our SHEQ Department maintains a Training Matrix, which ensures all qualifications are in-date and that every operative is experienced in the duty they are carrying out. It also allows operatives to have a training plan to encourage development and increase motivation.
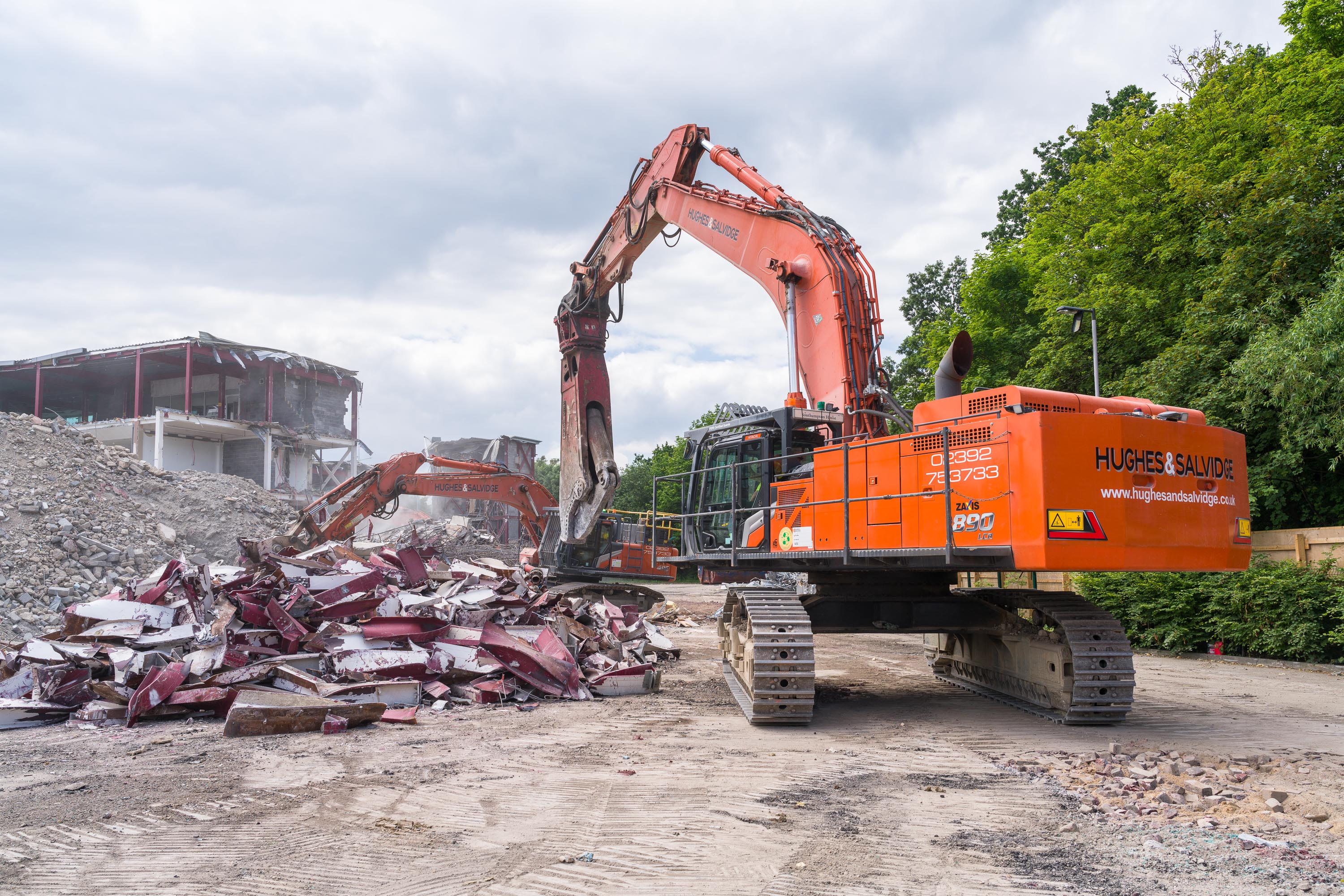
4. Monitor noise, vibration and dust
Environmental safety is also paramount on a demolition project. Noise, vibration, and dust are common by-products of demolition work, so they must be effectively monitored and managed to avoid any risk to the workforce or neighbouring properties.
Frequent exposure to loud noise can permanently damage a person’s hearing. In addition to this, noise can also create a safety risk, making it difficult for workers to communicate effectively or preventing them from hearing warning signs.
Vibration also poses a risk. The vibrating hand tools commonly used in demolition can cause hand-arm vibration syndrome (HAVS). As a result, workers’ exposure to vibration must be managed and reduced as much as possible.
Regular noise and vibration monitoring are conducted throughout all our projects with reports being issued to the client’s project team. Working hours can also be adjusted to ensure avoidable ‘noisy’ activities are undertaken at times that have minimal impact on the public.
Throughout the demolition process, we keep noise to a minimum in various ways:
-
Using correct plant for specific tasks and ensuring the plant is fully maintained.
-
Using ‘quietest’ method when both demolishing structures and removing hardcore and concrete, i.e. using bucket or pulveriser rather than impact breakers.
-
Leaving part of the external envelope of particular buildings intact whilst removing materials.
-
Ensuring works are only carried out within agreed working hours.
We invest in dust suppression methods, which involve the application of liquid to effectively restrict the airborne dissemination of fine particles. The water captures airborne dust particles, causing them to fall to the ground rather than disperse into the air. We utilise a dust suppression system that uses atomised misting equipment, which creates a water curtain, preventing the dust from being released into the air where it can become problematic.
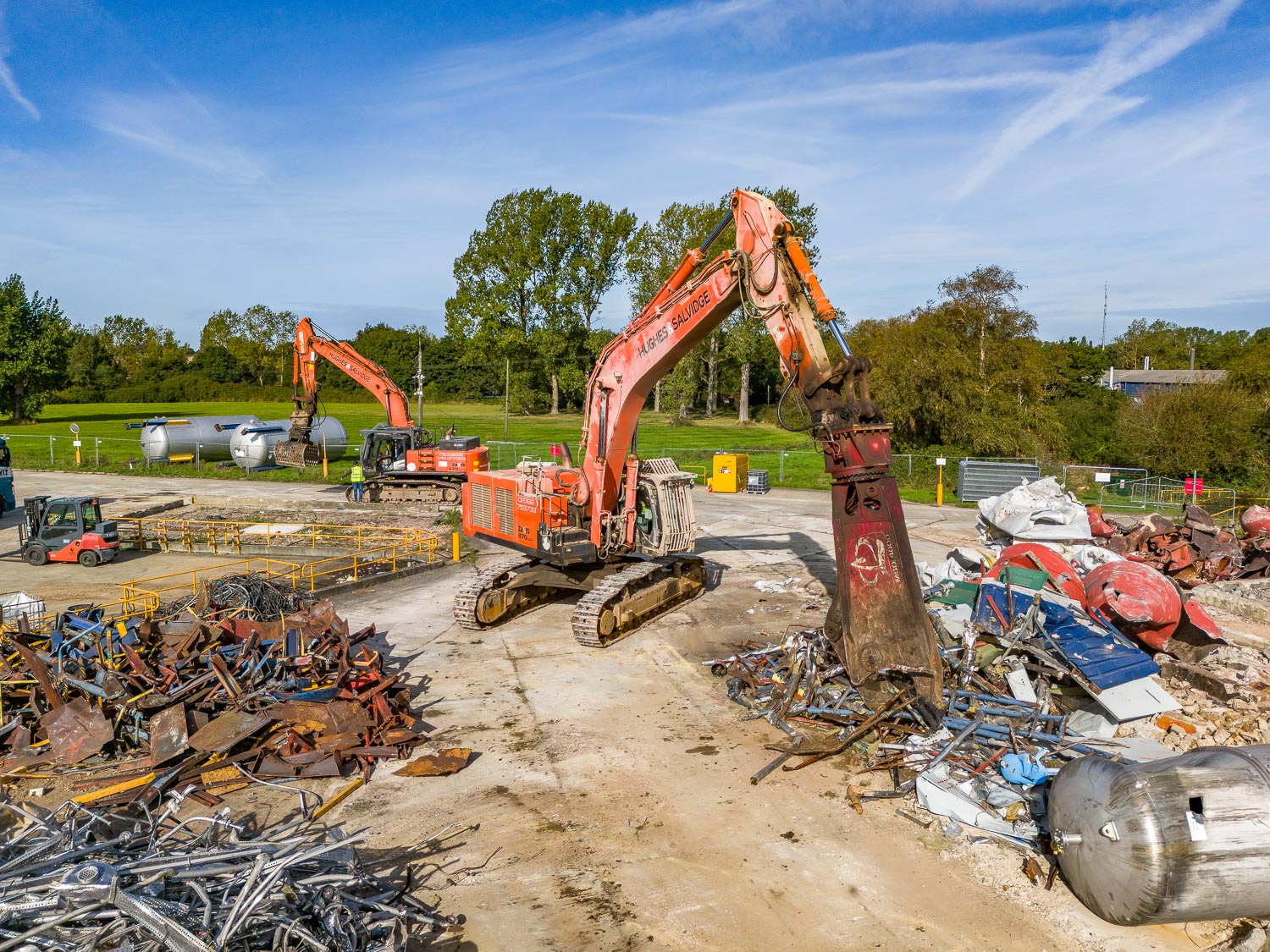
5. Keep the site clean
Keeping the site clean and safe throughout the demolition process is essential. A safe site also means ensuring that everyone has access to fresh drinking water and washing facilities, as well as hot water and a clean, safe environment for breaks.
At the tender stage, one of our management team will assess the welfare requirements that will be needed. When Hughes and Salvidge are Principal Contractors, we favour building our own welfare compound on-site. This will provide:
- Drinking water and hot water
- Lavatory and washing facilities
- Facilities to change and store clothing
- Storeroom for PPE, etc.
- Refuge against extremes of weather
- Generator to provide heating and lighting
- Separate messing facility with seats and tables
- Kettle and microwave
Health and safety information will be displayed on a notice board in the mess room. The following items will be displayed:
-
General Site Safety Rules
-
Emergency Rules
-
Map to Local Accident and Emergency Hospital
-
Identity of First Aider on-site
-
Location of First Aid supplies
-
HSE Law Poster
-
Health and Safety Policy Statement
-
Environment Policy Statement
-
Quality Policy Statement
-
Insurance certificate
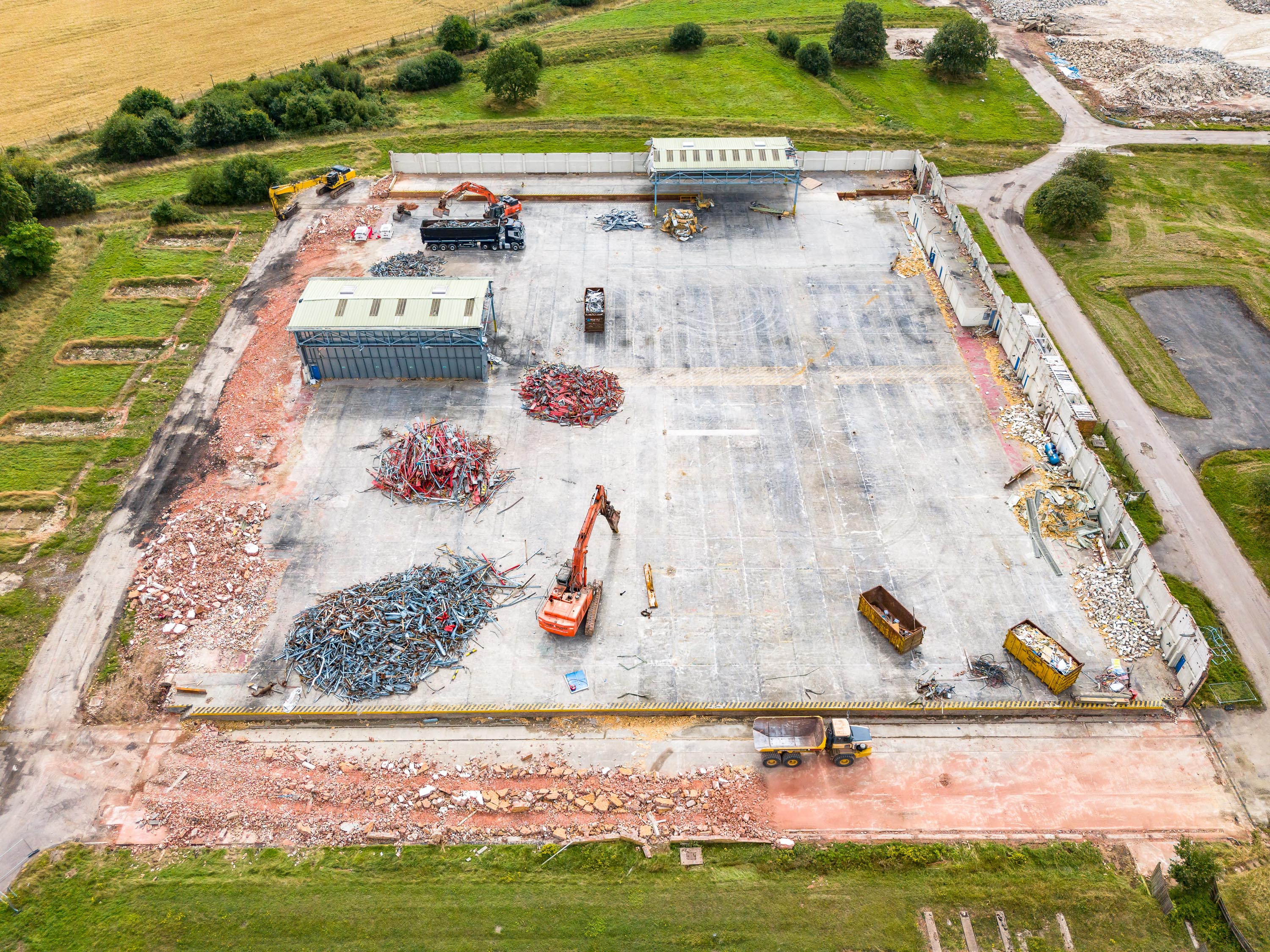
6. Manage traffic movement
To avoid putting workers at risk of being hit by vehicles turning, slewing, or reversing, effective traffic management systems are essential on-site. Wherever possible, vision aids and zero tail swing machines should be used. Traffic Management Plans are established during the planning phase of a project and updated/amended as the works commence and progress on-site.
Segregation of pedestrians and vehicles is implemented, giving clear and unhindered pedestrian walkways and vehicle access to all required areas of the site. Gatemen assist with flow and control of traffic on-site and a strict speed limit of 5 mph is enforced.
One-way systems are established to minimise the need for reversing and reversing cameras are on vehicles and plants to eliminate the need for operatives to be near vehicles. Furthermore, traffic movements (including deliveries) are timed to avoid rush hour traffic at both ends of the day so no queuing of construction traffic will occur.
7. Risk Assessments and Method Statements
Risk Assessments and subsequent Method Statements are fundamental elements in the safe planning, preparation and undertaking of a project. Upon award of a contract, Hughes and Salvidge have a structured approach to ensure the provision and control of safety from project conception to completion, taking into consideration the pre-construction information and other relevant documents provided at the tender stage. Before commencing the works, a pre-start meeting/tour of the site will take place.
The Site Manager/Supervisor, Contracts Manager, and SHEQ Manager walk the site and list all risks that are associated with the works. These are then recorded and written up into a Risk Assessment document. Method Statements are then produced based upon controlling the risks.
Regular site visits by the Contracts Manager and SHEQ Manager also ensures that work is being carried out in accordance with the approved Method Statement. All activities undertaken by Hughes and Salvidge are following the approved programme of work, phased operations and safe demolition techniques and the activities will be planned and undertaken in line with the Risk Assessments, Method Statements, Project Health and Safety Plan and Environmental Plan.
8. Maintain communication throughout
Your employees are key to understanding the risks on-site, so everyone must be involved and know what precautions are to be taken. When employees are involved in making decisions about health and safety, the workplace is safer.
Communication with a client, company management, site operatives and neighbouring residents or businesses are key to maintaining safety on-site. We ensure that all Health and Safety information is collated and passed on to a client for incorporation into the Health and Safety file. On-site, Health, Safety and Environmental information is disseminated to the site team to ensure maximum communication, education, and awareness.
Methods include:
- Daily briefings
- Tool Box Talks
- Company Memos
- Presentations
- Seminars
- Pre-Construction Information
- Health and Safety Plans
- Method Statements
- Risk Assessments
- COSHH Assessments
- Permit to Work
All site operatives and sub-contractors are issued with the Risk Assessments and Method Statements, providing them with the opportunity to comment on any potential issues before signing. At Hughes and Salvidge, we listen to our operatives and site staff as they are at the forefront of our operations. We have an ‘open door’ policy and encourage feedback and suggestions for improvements. Our management team conducts regular site visits to ensure standards are being upheld.
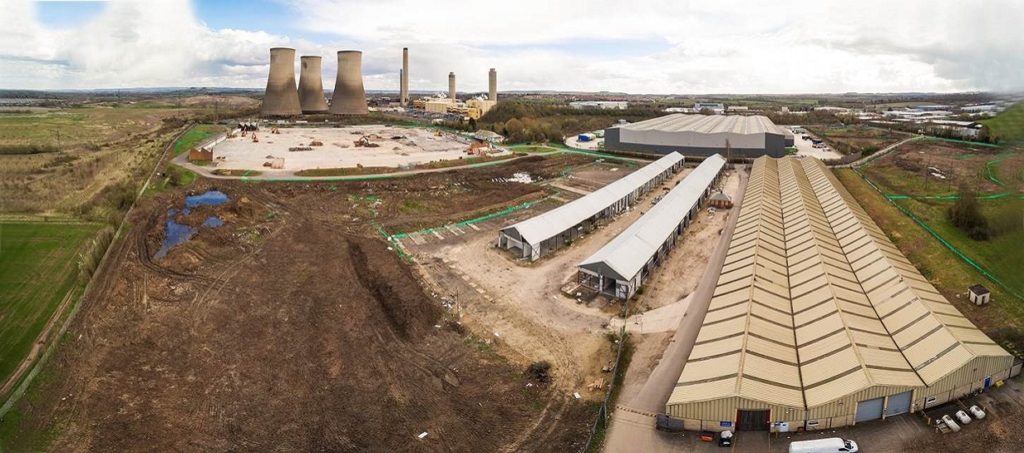
9. Manage waste disposal
Waste streams are identified as part of the risk assessment process and are a key safety measure on a demolition project. The control measures required are then selected to ensure that on-site techniques, which assist the segregation and containment of the different materials, are used. Contingency plans are also made at this stage as to what precautions should be taken to minimise the potential for harm to be caused in the event of a spillage or other form of release.
To fulfil the duty of care as a producer, Hughes and Salvidge ensure that all waste is properly identified, accurately described, and labelled before it is passed onto the waste disposal carrier. If the waste produced is of a complex nature, we may employ specialist external resources to advise on the identification and disposal methods to be employed. If appropriate, samples of waste will be taken for laboratory chemical testing. From these results, safe disposal options can be based and evaluated.
We ensure that a waste management licence for that specific waste type covers the chosen disposal facility and that the site has sufficient capacity to receive the waste. All controlled and hazardous waste, by definition, will be handled, processed, packaged, and disposed of in line with current approved codes of practice, associated legislation, Hughes and Salvidge-established procedures, and client-documented systems.
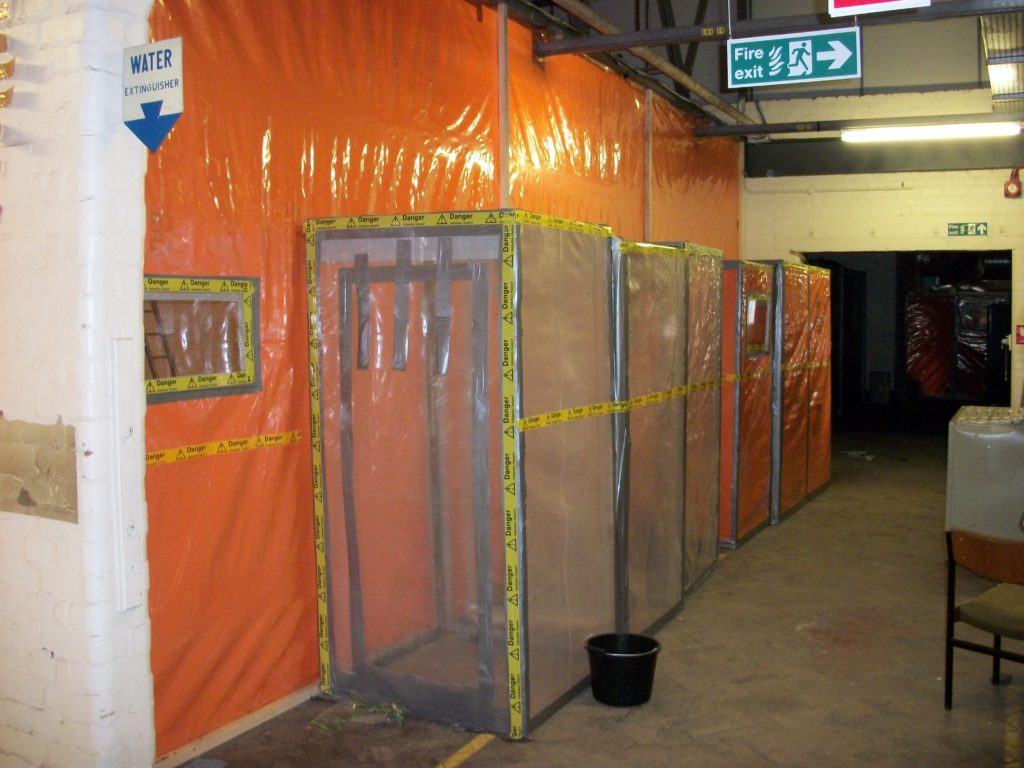
10. Follow regulatory safety measures
UK law also states ways that demolition must be carried out in a safe manner. The law discusses how demolition must be carefully planned and carried out in a way that prevents danger, by practitioners with the relevant skills, knowledge, and experience. According to HSE, the key issues to be aware of are:
Falls from height
During the demolition process, workers can be injured by falling from edges, or through openings, fragile surfaces, and partially demolished floors. Duty holders are responsible for assessing, eliminating, and controlling the risk of falls from height.
Injury from falling materials
Injuries can also be caused by falling materials resulting from the premature or uncontrolled collapse of structures. Duty holders must take the necessary steps to protect workers and passers-by from the risks posed by falling materials.
Uncontrolled collapse
The method statement for the demolition should identify the sequence needed to prevent the accidental collapse of the structure, considering the age and type of the structure, its previous use, nearby buildings and structures, and the weight of machinery being used.
Risks from connected services
Connected services, such as gas, electricity, water, and telecommunications must be isolated or disconnected before demolition work begins. Any services that cannot be disconnected should be clearly labelled to ensure they are not disrupted.
Hazardous materials
Hazardous materials such as dust, asbestos, and respirable crystalline silica must be considered, as well as any other material or contaminations on-site that have not been cleared.
Fire
During any structural alteration or demolition, fire is a risk. The fire plan must, therefore, be kept up to date as the escape routes and fire points may change at various points during the process.
Check out the demolition services we offer or get in touch to discuss your requirements with us.